日前,由宝钢工程技术集团宝钢技术自主集成研发的国内首台数字化、高精度、高效率焊管检测设备系统交付使用。据国内权威机构鉴定,该设备系统的高动态分辨率和射线透照质量达到了国际焊管检测最高等级的B级水平,成为国内首台达到“欧标”要求的设备。
随着石油天然气产业的长足发展,用户对石油天然气长输管的质量要求越来越高,因而检验标准也不断提高。业界传统,普遍采用对焊管焊缝X射线模拟成像的方法进行探伤检测,存在拍片检验速度慢、精度不够、洗片处理麻烦、伪缺陷多、底片质量波动等缺点,同时存在冲洗底片耗材费用高、洗片废液污染环境等不足,上述问题成了制约焊管质量提高、产能提升和进一步发展的瓶颈。
焊管探伤检测急需一种更精密、更高效和更环保的方法来替代。去年下半年,宝钢技术成立了攻关团队,全力推进数字化焊管检测系统开发工作。在没有现成技术可借鉴的情况下,攻关团队首先按照数字化的要求对硬件设备的工艺技术进行设计和不断改进优化,同时,结合数字技术进行软件设计,先后开发出了端口连拍功能、自动拼图功能、焊管通过算法、射线源对中和降噪等技术。经过一年多的技术开发和反复试验,首台数字化、高精度、高效率焊管检测设备系统诞生。
新的焊管检测设备系统可数字化一次完成焊管中间焊缝高速高清动态数字成像。这一变化,就像病人从拍X光片变为拍CT,检测速度和检测精度分别提高50%和20%。同时,避免了原检测方式对环境的污染和对操作人员身体的损害。检测技术的数字化,使宝钢成为目前国内焊管探伤检测唯一可以达到射线透照质量等级B级的企业,能够满足欧洲用户的生产要求。
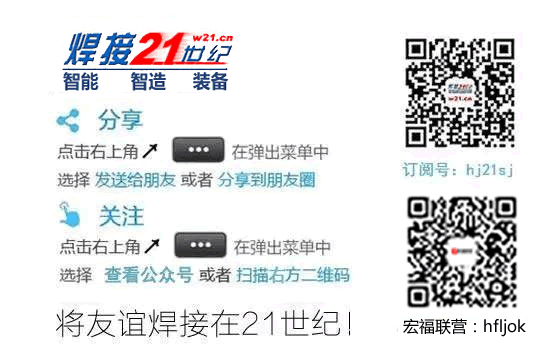 |