摘要:介绍了自行设计开发的微机控制的脉冲+,- 焊电源控制系统。研究分析了在脉冲MIG焊接中的PID控制算法。为了在焊接过程中实时采样、显示焊接参数,着重介绍了如何改进对串行器件MAX7219的编程,以及对PID控制算法的优化。试验结果证明,优化后程序执行效率高,响应速度快,控制精度高,可以实现稳定的脉冲MIG焊接过程。
关键词:逆变电源;PID控制;串行器件;80c196KC 引 言
PID控制器,又称为PID调节器,是工业控制中常用的校正装置。它结构简单,技术成熟,对被控对象的精确数学模型要求不高,调节参数可以根据现场调试或经验确定。因此广泛应用于连续控制系统中。
在微机控制系统中,对模拟量进行检测、转换、处理、计算等工作也是为了满足控制系统的要求。随着计算机技术的发展,特别是微机在控制中的应用,PID控制器已转变为PID控制算法,通过编制软件在微机上实现控制。减少了硬件开支,降低了成本,实现了以“软件代替硬件”的设计理念,从而使PID控制器迈上一个新台阶,使其应用更加广泛。该研究针对微机控制IGBT脉冲MIG逆变焊接电源控制系统脉冲控制程序的优化设计进行了研究和探讨。
1 微机控制脉冲MIG焊机控制系统
该控制系统以高性能16位单片机80C196KC为核心,系统的整体结构如图1所示。系统采用脉宽调制方式(PWM)调节弧焊电源的输出特性,通过焊接负反馈,采用PI控制算法,实时控制PWM的脉宽,使得电流输出值与给定值趋于一致。单片机首先根据预置的脉冲频率f和占空比D,计算基值时间Tb和峰值时间Tp,将其存入内存单元。引弧后,实时采样电流值,并与预置的基值电流(给定值)进行比较,根据误差进行PI控制,使电流输出值与给定基值电流趋于一致;待基值时间结束后,单片机再将采样到的电流峰值与预置的峰值电流(给定值)进行比较,同样根据误差,进行PI控制,使输出的峰值电流值与给定峰值电流趋于一致;待峰值时间结束后,再切换为基值。这样循环往复进行控制,就可以得到脉冲电流。
实现上述功能的单片机闭环控制系统如图2所示。单片机接收、处理数字量,采样到的电流经放大后首先进行A/D转换为数字量输入给单片机。单片机接收到该数字量后与给定值进行比较并采取相应的运算,将计算后的控制量(数字量)经A/D转换后送入脉宽调制芯片SG3525,输出2路互不重叠的脉宽信号,经过IGBT专用驱动芯片EXB841功率放大后,分别驱动2组IGBT,并使其交替导通,从而实现功率的输出。
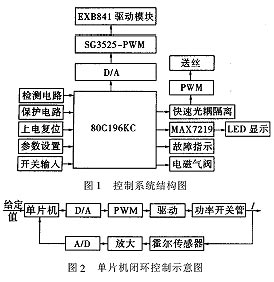
2 PID控制算法选择
在连续调节控制系统中,比例(Proportion)调节是最简单的一种。只要被调量偏离其给定值,比例项就会起作用,及时、有效地抑制干扰。比例调节的缺点是存在静态误差,消除静态误差的方法是在调节器中加入积分(Integration)环节。但是积分作用存在错误的半周期调整,会使系统的过渡时间延长,甚至造成系统不稳定。因此在实际生产中总是把PI 结合起来构成PI控制器。此外,还有微分(Differentiation)调节,微分项可以根据误差的变化趋势产生强调节作用,将误差尽快消除在萌芽状态,加快系统的动作速度。但是它对静态误差毫无抑制作用,所以只能与PI调节器结合起来构成PID调节器。PID调节器的传递函数为:

式中Kp为比例系数,Ti为积分时间常数,Td为微分时间常数。
将比例P、积分I、微分D3种调节规律有机结合,即可达到快速敏捷、平稳准确的调节效果。
将式(1)经过拉氏反变换,可求得时域内理想的PID控制算式:

为了在计算机上实现PID控制,需将式(2)离散化,以求和代替积分,用差分代替微分。设采样周期为T,PID控制算式的离散形式为:
 同样,可列出第n-1 个采样时刻的控制输出量:
 式中Ki=Kp*T/TI,为积分系数;Kd=Kp*T/Ti,为微分系数。 |