3.2优化的脉冲控制程序
通过分析MAX7219的工作时序发现,虽然MAX7219能够接收的数据和命令格式为16位的数据包,但是这16位数据包并不是1次传送而是分2次传输的,每次传输8位数,其中前8位用来选择MAX7219的内部寄存器地址,后8位为命令或显示的内容。显然,只要保证地址寄存器不被修改,间隔很短的时间(1s),后,再把后8位数据传到地址寄存器中,显示就不会出错。因此,将程序作了如下的优化:
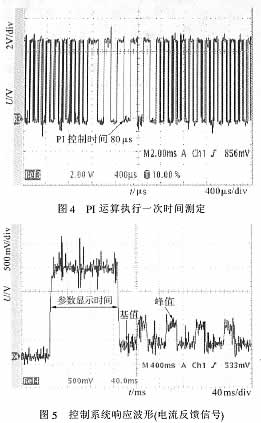 a. 更新显示时,不要1次同时更新5位LED的数值,每次只更新1位数码管的显示内容。
b. 16位数据传送时,先传送前8位地址,然后马上进行1次PI控制,控制时间仅为80μS,然后再传送后8位数据,这样既保证了显示又保证了系统的稳定性。
c.每进行200次PI控制后(所需时间约为16ms),再更新1位数码管显示。由于人眼视觉的暂留作用,在实际焊接过程中,即使每2s更新1次显示内容也不会给人频闪的感觉。
d.系统开始工作时总要经历几个周期的振荡才能达到稳定状态。PI参数需要通过大量实验整定,但是对于数字PI算法,控制灵活,无需对PI参数进行精确整定。所以程序设计时有意在系统刚开始工作时强制系统输出1个较小的值,这样可以减少系统的冲击,增加系统可靠性。经过优化的脉冲控制程序如下:
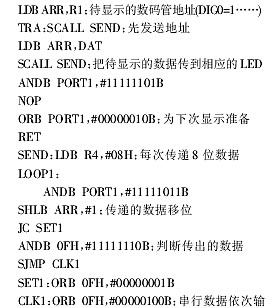
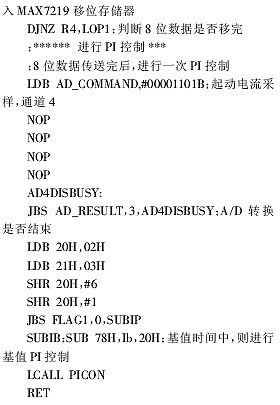
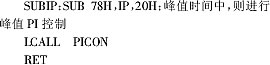
优化脉冲控制子程序后,进行联机调试表明焊接参数实时显示正确,无闪烁现象。测出系统的响应曲线(电流反馈信号)如图6所示,系统实现了稳定的焊接。
4 结 论
a. 整个控制系统采用以高性能的80C196KC单片机为核心,配以集成度高的专用芯片进行控制,并在整个控制电路的各个环节采取了多种抗干扰与保护措施。试验表明,系统电路简单,抗干扰能力强,工作稳定可靠。
b. 通过对脉冲控制程序的优化,控制系统的响应速度明显加快,控制精度提高。可以进行焊接参数的预置与实时显示,人机对话明了,操作方便。
c.采用优化脉冲程序可以实现稳定的焊接过程。

|