3、安装要求
3.1对P91钢的管道系统施工采用单方向施工,即至少总保持一端为自由伸缩端,以便于减小管道系统的应力,防止焊接是产生裂纹。 3.2对口装配全部采用机械对口卡具,绝不允许采用门型块电焊固方法进行焊口点固。 3.3严禁在坡口及管道上任意引弧和电弧擦伤。 3.4采取有效的防风、防雨措施,严禁在雨、雾等不良天气条件下进行焊接及热处理工作,以防止冷裂纹产生,提高焊接质量。 3.5必须保证焊接、热处理的连续性,避免由于以外断电导致焊接及热处理非正常中断。现场配备两路专用电源,其中一路为备用。 3.6 充氩装置需要耐高温,要有较好的密封性,并且易于取出和安装。在整个预热、焊接、热处理过程中,保留充氩装置,即可防止管道内穿堂风,又可在焊接区域形成封闭气室,起到保温和减小内外壁温差的作用。若出现不合格焊口,而且缺陷出现在根部或近根部,则焊缝进行返修时,仍需充氩保护。 3.7 P91钢焊接时最低环境温度应在5℃以上为宜,环境温度低于此温度时,严禁焊接,必要时一定要采取特殊措施。
4、焊接、热处理工艺
4.1首先按照《火力发电厂锅炉、压力容器焊接工艺评定规程》SD340—89的有关规定做好P91钢的焊接工艺评定工作。 4.2根据焊接工艺评定报告,编制出P91钢焊接工艺卡及焊接作业指导书。 4.3挑选出焊接工艺技术水平高、工作责任心强的高压合格焊工进行P91钢焊接培训并合格。正式施焊前,对焊工进行短期的焊前适应性培训,重点为氩弧焊打底练习。 4.4设立专门的焊条烘烤箱和专门的焊接材料发放记录,确保焊接材料的正确发放和使用。 4.5采用跟踪预热,最低预热温度不低于200℃。层间温度保持在300℃以下。 4.6采用Ws/D焊接工艺,并且进行两遍氩弧焊打底,保护气体氩气纯度≥99.995%,氩气流量为8—12L/mm。焊接材料使用9CrMoVN焊丝和BS24939Cr MoBH(AWS A5.5 E9016—B9)焊条。焊接线能量控制在30KJ/cm以下以保证焊缝冲击韧性。第一层氩弧焊打底厚度不允许低于3mm,由于P91钢焊接时,熔池铁水粘度大,流动性差,焊接规范又小,因而容易出现夹渣,层间未熔合等缺陷,因此为避免大的缺陷产生及保证焊接接头的综合机械性能,必须采用多层多道、小规范进行焊接,焊层厚度尽量减薄,每层焊道厚度不超过焊条直径的2mm;摆动焊接时,焊条摆幅不超过焊条直径的4倍,每层焊道必须清理干净,尤其注意清理接头及焊道两侧,焊缝外表焊接完毕,要求焊工立即进行清理自检,发现外表成形不好的马上补焊,严禁在焊缝冷却后再直接补焊。
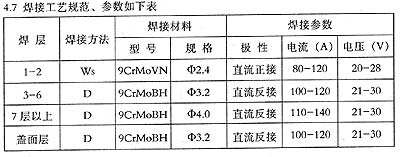
4.8采用背面充氩保护工艺,以避免焊缝根部氧化,背面充氩保护气体纯度≥99.995%,流量为3—25L/min。不仅第一遍打底时需要进行充氩保护,而且第二遍氩弧焊时,仍要继续进行充氩保护。充氩装置根据管道具体情况而。 4.9焊接完成后必须进行后热处理,后热处理温度控制在300—350℃,并保温2小时。 4.10焊后热处理采用多路输出、多点测温,且加热器与热电偶一一对应,焊口上、下温度始终保持一致,使热处理焊口在升、降温度以≤150℃为宜。加热温度为750—780℃,恒温按每25mm壁厚/1小时计算,但最少不得少于3小时。降温至300℃时,可不控制,冷却至室温。 4.11加强对P91钢焊接过程的控制工作,从措施、人员、材料、设备、对口、焊接、热处理参数、焊接接头表面质量、无损探伤、缺陷焊缝的返修等各方面进行控制。 4.12焊口返修必须采用机械方法(磨光机打磨)消除缺陷。 4.13为确保将缺陷彻底清除,打磨后请实验人员对缺陷清除情况进行确认清楚干净后方可进行补焊,补焊工艺与正式焊接相同。
5、结 语
5.1通过采取以上安装顺序,消除了焊接应力,保证了管道系统的正常运行。 5.2通过采取以上焊接工艺,焊缝外观工艺质量和内在质量得到全面控制,外观质量全部达到优良标准,所有焊口经100%磁粉、超声和射线探伤全部合格。 5.3通过采取以上预热、热处理工艺,焊接接头表面硬度全部达到标准要求,证明焊接接头冲击韧性合格。 5.4通过采用背面充氩保护工艺和合适的充氩装置,保证了焊接接头根部质量。 5.5为工程施工焊接过程控制及记录要求探索出新的经验。
|