1.3 电源的基本参数
输入电压:380V/50Hz;输出****功率:6kVA;****空载电压:200V(切割)、80V(焊接);输出电流:0-30A(切割)0-60A(焊接);负载持续率:60%。
2 单片机控制与显示电路
2.1 控制与显示功能简述
电源工作时,控制与显示电路的功能是对主电路的电压、电流和气压进行显示,并通过中断控制气路的接通,控制高频的产生和1s之后的断开,同时通过检测电流是否为零,控制气路的断开。具体的控制顺序为:
合上控制电源开关KB2,控制电路接通,XD1灯亮,单片机进入工作状态。此时按一下起弧开关,单片机在中断程序控制下打开电磁阀,气路接通,当气压达到0.4Mpa(YJ压力继电器气压调正值是0.4Mpa),YJ触点闭合,这时合上电源开关KB1,主电路接通,数码显示空载电压为200V(切割)或80V(焊接),气压0.4Mpa; 以上。待一切参数正常后,再按下起弧开关QHK,单片机再次进入中断程序,控制接通高频振荡器1GJ2,此时等离子割炬%或焊枪&在高频电压的作用下(2500V、250kHz)击穿电极与喷嘴之间的空气,形成等离子弧。高频振荡器工作1s后,自动断开,此时30A切割(焊接为60A)电源进入切割(或焊接)状态,电流显示30A(或60A焊接)。当切割(或焊接)完毕时,割炬或焊枪所带阴极电压离开带阳极的工件,等离子弧自动熄灭,这时单片机检测到的电流值为0,在延迟程序的控制下,30s后气阀自动关闭。
2.2 控制系统
电路原理如图4所示,电压、电流、气压信号分别由电压、电流、气压传感器接入,经变送器转换成统一的0-5V的模拟信号,再经采样、A/D转换后送至单片机进行实时处理,其结果送至扩展I/O接口电路进行数码显示。同时,I/O接口电路还分别输出开关量信号经光电耦合后控制高频起弧和气阀开关。为了防止外围设备对主机的干扰,该系统采取了光电隔离措施,从而提高了系统的稳定性[1]。
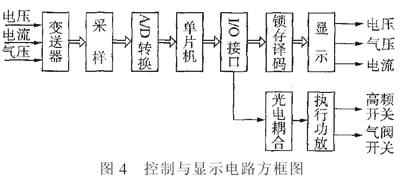
2.3 控制系统设计
控制电路如图5所示,基于MCU功能、价格、便捷性等多种因素考虑,系统采用了MCS-51单片机51系列中的8031芯片,由于8031内部没有EPROM,所以扩展了一片程序存储器2732A芯片,便于用户随时修改程序[2]。电压、电流、气压传感器输出信号是0-5V连续变化的模拟信号,通过A/D(ADC0809)转换器把这些模拟信号变成数字信号送到单片机进行处理。处理后的结果送至可编程的并行I/O接口芯片8225A进行显示和输出控制(打开气阀或接通高频引弧)。8225A(1)的A口和B口显示电压参数(3位),8225A(2)的A口和B口分别显示电流(2位)和气压(2位)参数,C口的PCO输出信号控制高频引弧,PCI输出信号控制气阀开关[1]。
为了直观、方便地读取各参数,系统采用静态显示方式,即每位参数选用一片74LS47译码锁存芯片和一块LED发光二极管显示器。控制信号8225A(2)的输出经74LS06反相器送至光电隔离管输入端,光电管的输出信号由NPN管组成的功放电路放大,从而驱动继电器J1和J2打开或关闭气阀。图5中的U4-U7(74LS373)分别锁存ADC0809、732A、8255的地址线[3]。
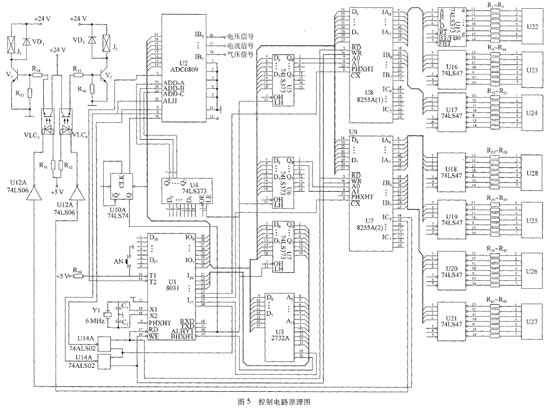
3 系统程序设计
3.1 程序流程图
单片机控制和显示电路的程序设计流程图如图6所示。
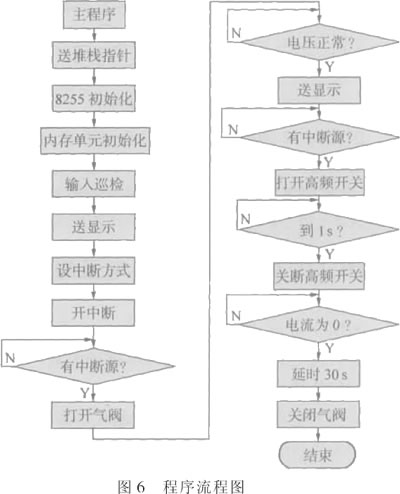
3.2 地址分配
片选:P2.4 8225A(1) DFFCH-DFFFH P2.5 8225A(2) EFFCH-EFFFH P2.6 2732A BFFFH
数据采集单元地址:(信号输入都0-5V)
电压输入:IN0 7FF8H 电流输入:IN1 7FF9H 气压输入:IN2 7FFAH
内部RAM地址分配:
采集单元次数: R7 采集数据缓冲器: 50H-67H 采集通道: R6 堆栈指针: 30H 中断入口: 0013H(INT1)
参考文献:
[1] 何立明。MCS-51系列单片机应用系统设计配置与接口技术[M]北京:航空航天大学出版社,1990 [2] 张友德,赵志英,涂时亮。单片微型机原理、应用与实验上海:复旦大学出版社,1999 [3] 潘新民,王燕芳。微型计算机控制技术[M]北京:人民邮电出版社,1999
|