前 言
激光焊接过程的监测主要是基于声、光、电、热等信号监测焊接过程中气孔等缺陷的形成,但对未焊透时焊缝的成型状况特别是焊缝熔深则缺乏有效的监测,这主要是由于很难在熔深和监测信号之间建立一个稳定、直接的映射关系。在过去对熔深的监测中多采用“黑箱”模型——将监测信号和实验所测的焊缝熔深直接拟合得到监测信号与熔深之间的映射关系或者采用人工神经网络来建立二者之间的对应关系[1, 2]。
同轴视觉传感是一种先进的激光焊接过程监测方法,可以实现焊接过程中的可视化、直接监测。但是由于激光致等离子体和金属蒸气对熔池和小孔的覆盖,使得在对激光深熔焊接过程同轴视觉传感监测过程中观测不到小孔的底部,并且小孔同轴图像灰度值的变化也不能表征小孔深度的变化[3, 4]。因此不能利用图像三维形状恢复技术和小孔同轴图像灰度值与焊缝熔深的标定曲线来实现激光深熔焊接过程中焊缝熔深的监测。
尽管小孔的同轴视觉图像不能反映出小孔底部的三维形状和深度信息,但仍然能够反映出小孔底部的径向形状和大小[3, 4]。因此可以通过图像处理提取出小孔的径向尺寸。本文在提取出小孔径向尺寸的基础上基于Nd:YAG激光深熔焊接过程中小孔前壁材料蒸发满足的能量条件来求解小孔的深度,并基于所提取出的小孔的深度实现了激光深熔焊接过程中焊缝熔深的直接监测。
本文中焊缝熔深监测是基于图像处理结果和焊接过程中小孔前壁满足的能量平衡进行的,不依赖于等离子体的辐射光强,是一种直接监测的方法。
1 实验条件 实验用的激光器是额定功率为2 kW的Nd:YAG固体激光器,输出波长为1.06 μm的连续波激光,激光束由内径为0.6 mm的光纤传输,经焦距为200mm的透镜聚焦后的激光束焦点直径为0.6mm;工件为250×100×1.8 mm 的Q235钢板,同轴保护气为Ar气。
小孔同轴视觉图像的采集采用自主开发的Nd:YAG激光焊接过程同轴视觉传感系统[7]。同轴视觉传感系统组成框图如图1所示。
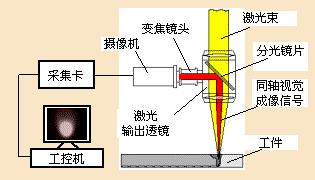 图1 同轴视觉图像采集系统组成框图
对所采集的小孔和熔池的同轴视觉图像,经平滑滤波除噪和同态滤波增强的预处理后,基于阈值分割技术提取出小孔和熔池的边缘,利用Hough变换拟合得到小孔内外边缘的曲线方程,从拟合结果中得到小孔的径向尺寸。所采集的小孔同轴图像及小孔边缘Hough变化拟合结果如图2所示。
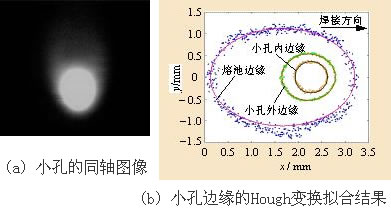 图2 小孔同轴图像及小孔边缘Hough变换拟合结果
2 小孔前壁的能量平衡 在给定焊接规范下,当焊接过程达到稳态时,小孔也达到了动态平衡状态:小孔深度和焊缝熔深不再变化,接受激光束辐照的小孔前壁材料不断熔化和气化,孔内脱离激光辐照的金属等离子体不断复合成金属蒸气并和孔内未电离的且不在激光辐照区域内的金属蒸气一起液化形成小孔的后部。这样随着激光束在工件表面上的连续扫描,小孔前壁的材料不断气化,焊接过程不断地进行。小孔前壁受激光辐照的示意图如图3所示。
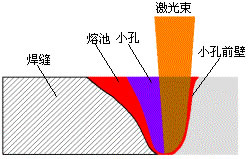 图3 激光深熔焊接过程中小孔受辐照的示意图
小孔前壁吸收的激光能量除了使材料达到气化状态并使金属蒸气具有一定的动能外,还有一部分能量通过热传导的方式传递到母材中去。因此小孔前壁不断气化满足的能量条件为: EA=EV + EK + EL (1) 式中:EA——被小孔前壁吸收的激光束能量; EV——小孔前壁气化所需要的能量; EK——蒸发后金属蒸气的动能,为能量损失; EL——通过热传导损失的能量。
由于金属蒸气的动能EK与材料蒸发所需要的能量EV相比很小,可以忽略不计[5]。由小孔经热传导传递到液态层和母材中能量EL和材料蒸发所需要的能量EV之间近似有如下关系[4]:
(2)
式中:ε——为热传导造成的能量损失与材料蒸发所需的能量之比; I——单位质量的材料蒸发所需要的能量; ——材料的比热; TV——材料的沸点。 因此,小孔前壁的能量平衡条件可简化为: EA=(1+ε)EV (3)
在激光深熔焊接过程中,辐照在小孔前壁的激光功率密度是小孔前壁材料蒸发的决定性因素;考虑到计算小孔前壁的体积及其消耗的能量需要较多的假设条件,将会产生很大误差。因此,以单位面积的材料蒸发所需要的能量密度为基础建立小孔前壁材料气化的能量平衡方程。
用功率密度表示的小孔前壁气化过程中满足的能量平衡方程为:
(4)
式中:A——工件材料对Nd:YAG激光的吸收率; Q——激光功率; R——激光光斑半径; ρ——材料密度; Vd——小孔前壁加深的平均速度。 在方程(4)中,只有小孔前壁平均加深速度是与小孔深度紧密相关的未知量。 3 小孔深度的求解
3.1 小孔平均加深速度的求解 小孔前壁的加深速度是由辐照在其上方的激光焊接体能量所决定的,其瞬时下降速度受各种条件的限制很难将其求出。因此,根据小孔的径向尺寸来求解小孔前壁的平均加深速度。
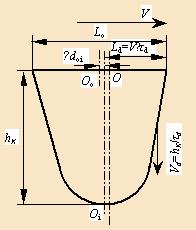 图4 小孔纵截面示意图
图4为小孔纵截面的示意图。假设小孔底部为半椭球面,短轴直径为提取出的小孔内边缘的宽,长轴直径为提取出的小孔内边缘的长,且小孔最深处的水平位置与小孔内边缘中心的水平位置重合。在τd时间内,小孔前壁的材料从工件表面加深至小孔的最深处,其深度方向上的位移为小孔深度hk,而激光束在焊接方向上对工件的扫描距离为Ld,则有:
(5) 式中:hk——小孔深度; Lo——提取出的小孔外边缘的长度; ∆doi——提取出小孔内外边缘之间中心距; V——为焊接速度。 则从(5)式可得小孔前壁的平均加深速度为:
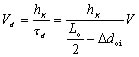 (6)
3.2 小孔深度求解方程的建立 将(6)式代入到(4)式整理可得小孔深度为:强度/(arb.units) (7)
将激光光斑半径R随离焦量∆z变化的拟合关系式R=11.56∙(∆z)2——+R0(R0为激光束焦点半径)代入上式[4],并考虑焊接过程中激光束焦点位置的偏移∆h,可得到小孔深度的求解方程:
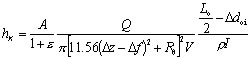
(8) 式中:∆f——焊接过程中激光束焦点位置的偏移量。
式(8)即为在激光功率为Q,焊接速度为V,离焦量为∆z条件下小孔深度的求解方程。从(8)式中可以看出,小孔深度由激光功率、焊接速度、离焦量等焊接规范参数及材料的热物理参数决定。此外,激光束焦点大小对小孔的深度也有一定的影响。
在激光深熔焊接过程中,小孔处在液态金属的包围中,小孔的前壁是具有一定厚度的液态金属层。因此,本文认为小孔前壁下降是从液态金属表面开始的。因此,(8)式中材料的热物理参数分别取ρ为材料液态时的密度,I为单位质量的材料从液态到气态的气化过程中所需要的能量,取材料的比热在材料熔点TM到沸点TV范围内的平均值为:
,则单位质量的液态材料气化所需要的能量I为:
(9) 式中:LV——为材料的汽化热; TM——为材料的熔点。
3.3 小孔深度的求解 小孔前壁为一倾斜的斜面,因此在小孔深度的求解过程中,激光功率密度不能按照辐照在工件表面的激光功率密度处理。鉴于小孔前壁加深速度为一平均值,因此小孔深度求解方程中的激光功率密度按小孔半深处的激光功率密度作为辐照在小孔前壁的平均激光功率密度处理。将小孔深度求解方程修正为:
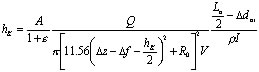
(10) 这样小孔深度求解方程变成一个5阶非线性方程,其根不能用根式或解析式表示[6],方程(10)需要用数值法求解。
对方程(10)的结构分析可以看出,方程(10)的右边可分为三项:第一项为系数项;最后一项与由同轴视觉传感监测提取出的小孔的二维径向特征参数和材料的热物理参数有关;而第二项是与焊接规范参数有关的项,物理意义为单位面积上的焊接线能量(或单位时间内激光功率密度),其被定义为焊接体能量。
焊接体能量qV的定义为[4]:
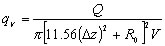 (11) 则方程(10)又可表示为:
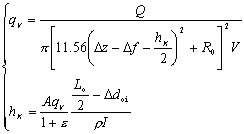
(12)
从(12)式中可以看出,在激光深熔焊接过程中,小孔深度的变化将会引起辐照在小孔前壁的焊接体能量的变化;反之,焊接体能量的变化又将导致小孔深度的变化,二者相互影响。因此,以(12)式为基础通过迭代可求得小孔深度。
4 基于小孔深度的焊缝熔深的监测 4.1 焊缝熔深的提取 由于孔底液态金属层的厚度很薄[4, 5],对焊缝熔深的影响不大,因此本文以小孔深度作为焊缝熔深来处理。则分别测量不同焊接规范参数下的焊缝熔深来验证由同轴视觉传感监测到的焊缝熔深。
4.2 焊缝熔深监测值的验证 图5、6、7、8分别为焊缝熔深的监测值和实验测量值随激光功率、焊接速度、离焦量及同轴保护气流量变化的曲线及其监测误差曲线。
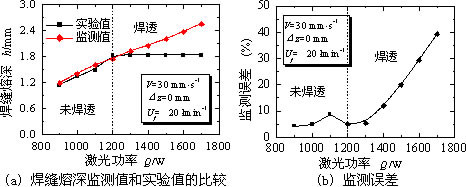 图5 不同激光功率下焊缝熔深的监测及其误差
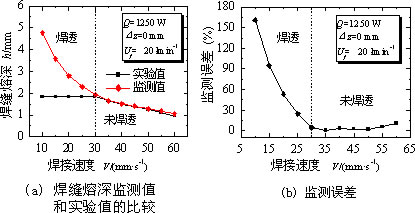 图6 不同焊接速度下焊缝熔深的监测及其误差
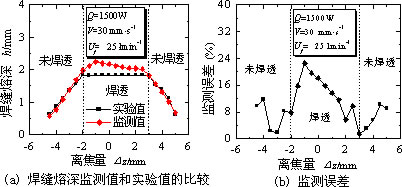 图7 不同离焦量下焊缝熔深的监测及其误差
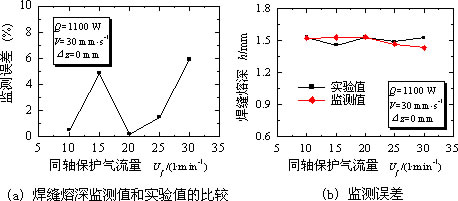 图8 不同同轴保护气流量下焊缝熔深的监测及其误差
从图中可以看出,在工件未焊透时,焊缝熔深的监测值与实验值具有较好的一致性,其监测误差****不超过12%,****误差为11.76%,而且是在不太常用的大离焦量下所监测到的;而在常用的小离焦量下,焊接规范参数的变化过程中未焊透时焊缝熔深的监测误差都不超过10%。较小的监测误差说明,工件未焊透时对焊缝熔深的监测是比较准确的。
在工件焊透时,焊缝熔深的监测值明显大于工件厚度,具有很大的监测误差。这主要是由于在工件焊透时有一部分激光束能量透过孔底液态金属薄层而损耗在工件之外,但在熔深监测过程中并没有考虑这部分能量损耗而造成的误差。另外,随着焊接体能量的增大,透过孔底液态金属层损耗的激光能量也就越多,造成的监测误差也就越大。
4.3 工件焊透的判断 由于工件焊透后焊缝熔深的监测值明显大于工件厚度,因此可以直接利用焊缝熔深的监测值和工件厚度比较来判断工件是否被焊透。
在实验过程中发现,当工件刚刚焊透时的焊缝背面成形并不是连续的,而是断断续续的,而这些不连续的焊点在对接的情况下将会成为裂纹起始点和应力集中点而成为焊接缺陷。因此本文将这情况列为未焊透的状态。为了避免在监测过程中对这种情况出现误判,本文在焊透的判断过程中预设一定的判断裕量。本文根据实验情况取工件厚度的8%,即焊缝熔深的监测值不小于工件厚度的1.08倍时,认为工件是完全焊透的,否则认为工件未焊透。
实验结果证明,在工件焊透状况判断过程中考虑一定的判断裕量提高了判断的准确性和可靠性。
5 结 论
在由同轴视觉传感监测提取出的小孔径向尺寸和小孔前壁材料气化满足的能量平衡的基础上推导建立了小孔深度提取的迭代方程。基于在同轴视觉传感监测中所提取出的小孔深度实现了Nd:YAG激光深熔焊接过程中焊缝熔深的直接监测和工件焊透的判断。
焊缝熔深监测值和实验测量值的比较表明,工件未焊透时,焊缝熔深的监测值和实验测量值具有较好的一致性,其监测误差一般不超过12%;而工件完全焊透后,焊缝熔深的监测值明显大于工件厚度。 在工件是否焊透的判断中,通过预设工件厚度的8%为判断裕量提高判断结果的可靠性和准确性,避免在工件刚刚焊透对焊缝背面不连续成形出现误判。
|