钛材在焊接时易出现的焊接区氧化、焊缝气孔、冷裂纹等质量问题,本文详细列出了具体可行的有效的预防措施。
1、气孔是钛焊接时最常见的焊接缺陷。
原则上气孔可以分为两类,即焊缝内部气孔和融合线气孔,在焊接线能量大时气孔一般位于融合线附近。气孔的影响主要在与降低焊接接头的疲劳强度,甚至无损探伤检查不出来的小气孔,对疲劳强度都会产生明显的不利作用。气孔能使接头疲劳强度降低一半甚至3/4,故此,焊接时不宜选择大的线能量,宜选用小电流,快速焊的工艺。
2、焊接接头的冷裂纹
氢是钛中最有害的元素之一,它能降低钛的塑性与韧性,导致脆裂。若母材或焊接材料中含氢量较大,则应预先作脱氢处理。钛在600℃以上就会急剧地和氧、氮化合,生成二氧化钛和氮化钛(硬度极大)。当加热到800℃以上,二氧化钛即溶解于钛中并扩散深入到金属钛的内部组织中去,形成0.01~0.08mm的中间脆性层。温度越高,时间越长,氧化、氮化也越严重,焊接接头的塑性就会急剧降低。 此外,钛还易与碳形成脆性的碳化物,降低塑性和可焊性钛材的熔点高,属难熔金属,在焊接时需要高温热源。钛的导热系数低,仅为碳钢的一半,热量不易散失,过热倾向严重。当结构刚性较大时,在焊接拉应力作用下,还会引发薄弱区开裂。另外钛沾染铁离子即变脆。这也是导致钛材对接焊缝区产生裂纹的重要原因之一。
3.根据多年来实际焊接经验,预防钛焊接时产生气孔和裂纹可采用以下措施:
(1)做好焊前准备。焊件和焊丝表面质量对焊接接头的力学性能有很大影响,因此必须严格清理。铁板及钛焊丝可采用机械清理及化学清理两种方法。 (a)机械清理:对焊接质量要求不高或酸洗有困难的焊件,可用打磨机、细砂纸、硬质合金刮刀或不锈钢丝刷擦拭,但最好是用硬质合金刮刀刮削钛板,去除氧化膜。 (b)化学清理:焊前可先对试件及焊丝进行酸洗,酸洗液可用HF5%+HNO335%的水熔液。酸洗后用净水冲洗,烘干后立即施焊。或者用丙酮、乙醇、四氯化碳、甲醇等擦拭钛板坡口及其两侧(各50mm内)、焊丝表面、工夹具与钛板接触的部分。清洗待焊件表面并在2小时内焊接。 正确选择焊接设备。根据焊接技术要求与技术规范,具体选择好相应的焊接设备。例如,进行钛及钛合金金钨板氩弧焊,则应选用具有下降外特性、高频引弧的直流氩弧焊电源,且延迟递气时间不少于15秒,避免焊遭受到氧化、污染。 (2)正确选择焊接材料。氩气纯度应不低于99.99%,露点在-40℃以下,杂质总的质量分数<0.001%。重要构件背面应冲氩气保护,当氩气瓶中的压力降至0.981MPa时,应停止使用,以防止影响焊接接头质量。原则上应选择与基本金属成分相同的钛丝,焊丝以真空退火状态供应。有时为了提高焊缝金属塑性,也可选用强度比基本金属稍低的焊丝。 (3)把握好焊接坡口。原则上应尽量减少焊接层数和焊接金属。随着焊接层数的增多,焊缝累计吸气置增加,以至影响焊接接头性能,又由于钛及钛合金焊接时焊接熔池尺寸较大,因此试件开单V型70°~80°坡口,且不作摆动。焊丝末端不得移出气体保护范围,喷嘴直径可适当加大以扩大保护区域。 (4)注意选择保护气体流量。气体流量的选择以达到良好的保护效果为准,过大的流量不易形成稳定的层流,并增大焊缝的冷却速度,使焊缝表面层出现较多的α相,以至引起微裂纹。拖罩中的氩气流量不足时,焊缝呈现出不同的氧化色泽;而流量过大时,将对主喷嘴的气流产生干扰作用。焊缝背面的氩气流量也不能太大,否则会影响到正面第一层焊缝的气体保护效果。总之,要控制好气体的流量及流速,防止产生紊流现象,影响保护效果。 (5)正确选择焊接工艺参数。增加深池停留时间使用时防止气泡逸出,可有效地减少气孔。同时,采用小电流、高焊速的焊接规范,焊接层数越少。
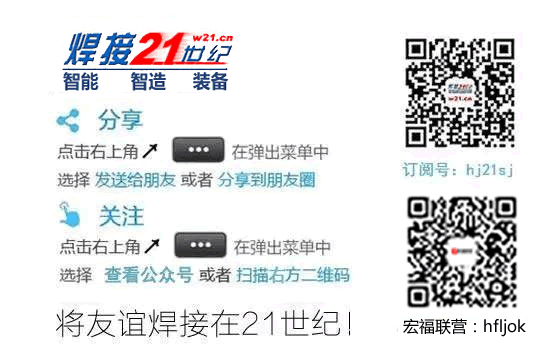
|