一、概述
随着科学技术的不断进步以及国内人工成本的逐步上涨,自动化焊接技术因其质量稳定、焊材消耗少、焊工培训周期短及劳动强度低等特点,在核电建设安装领域得到了一些应用,并取得了良好的社会和经济效益。 中国核工业二三建设有限公司(简称“中核二三”)作为我国规模****的核工程综合安装企业之一,近年来持续加大在核电安装技术革新方面的研发投入,取得了一些研究成果,本文将进行详细介绍。
二、全位置TIG自动焊技术
管道焊接是核电建造安装过程中工程量****的环节,单台百万千瓦级核电机组管道安装工程量近12.5万m。核电管道焊接质保等级高,对于质量要求严格,现有的焊接方法主要以TIG(钨极氩弧焊)为主,效率低,工程质量受焊工技能影响大,不易保证。因此,针对核电管道焊接采用自动焊技术是提高质量和效率,降低高技能焊工依赖度最有效的方式。目前,中核二三公司分别针对核电站一回路主管道和波动管,二回路主蒸汽和主给水管道以及核岛辅助管道预制,开展了自动TIG焊技术的研发,其中,主管道窄间隙自动焊技术已经在我国核电安装现场得到了成功应用。
1. 核电站主回路管道窄间隙TIG自动焊技术 核电站主回路管道是连接核电站反应堆压力容器、主泵和蒸汽发生器等主要设备的大厚壁承压不锈钢管道,被称为“主动脉”,承担着核安全保护屏障的重要功能,属于核电厂一回路压力边界,要在高温、高压的工况下运行40年以上,对焊接质量要求非常严格。以百万千瓦核电机组为例,单台机组共三个环路,每个环路8道焊口(见图1),主管道直径****976mm,壁厚97mm,单个焊口采用宽坡口手工焊技术需要焊接约1个月时间,焊材消耗量大,对焊工技能要求高。
 图1 中核二三公司于2005年启动了窄间隙TIG自动焊技术的研究工作,经过近5年的技术攻关,完成全套技术的研发。该技术与手工焊技术相比,单个主管道焊口的焊接时间仅10~15天,为手工焊的1/3~1/2;焊接材料消耗仅10~15kg,约为手工焊的1/8;自动焊工培训周期仅需2个月,约为手工焊的1/10;不仅缩短了焊接时间,降低了焊材消耗,而且大幅缩短了焊工培训周期,降低对于高技能焊工的依赖。 2011年,中核二三公司首次将这项技术在我国宁德核电主回路管道安装现场成功应用,并推广到红沿河、阳江、防城港、福清和方家山等核电项目(见图2)。目前,我国在建CPR1000、AP1000以及EPR堆型核电厂主回路管道安装焊接均采用了自动焊技术,取得了良好的经济和社会效益。
 图2 2. 波动管窄间隙TIG自动焊技术 波动管是稳压器实现主回路压力控制和超压保护的重要组成部分,整体呈螺旋状连接, 将反应堆冷却剂系统主管道热管段与稳压器下封头接管嘴相连。 以EPR核电堆型为例,波动管道材质为不锈钢,单机组波动管分7段安装,需现场焊接8个焊口(见图3),管径大、管壁厚,对焊接质量要求高。台山核电一期工程波动管安装首次采用了窄间隙TIG自动焊技术,焊口射线探伤一次合格率达100%,优异的焊接质量,为机组安全运行提供了坚实保障。目前,国内三代AP1000堆型波动管焊接也采用了窄间隙TIG自动焊技术。
 图3 3. 主蒸汽管道自动焊技术 主蒸汽管道是连接核岛蒸汽发生器与常规岛汽轮机的二回路大直径厚壁承压管道,由于其运行工况特殊,安全等级高,因此对焊缝质量要求高,是核电厂当中的大型超级管道。目前,我国在建二代核电技术,主蒸汽管道焊接采用手工TIG根部打底、焊条电弧焊填充盖面的焊接技术。而以AP1000核电堆型为代表的三代核电安装技术规格书要求,对于采用LBB(leakage before broken破前泄露)设计的主蒸汽管道焊接必须采用钨极氩弧焊(TIG)工艺。 以我国在建三门和海阳核电项目为例,主蒸汽管道材质为SA335—P11,管径965mm,壁厚44.2mm,属于耐热低碳合金钢,焊前需要预热,焊后需要进行消应力热处理,焊接难度大。采用手工TIG焊技术完成一道主蒸汽管道焊口,大约需要两名高级焊工在200℃的高温下连续焊接作业约20天,焊接效率低,劳动强度相当高。 为进一步提高主蒸汽管道焊接效率,中核二三公司于2013年启动主蒸汽管道窄间隙TIG自动焊接工艺研究,并于2014年底全部完成该技术研发(见图4)。与手工焊相比,采用该技术可使单道焊口的焊接时间由20天缩短到8天,焊材消耗由20kg降低到10kg,优势相当明显。
 图4 目前,该技术将在中广核红沿河5/6号机组安装现场进行首次成果应用,同时,该技术还可推广到在建的“华龙一号 ”、AP1000和CAP1400堆型主蒸汽管道安装现场。
4. 辅助管道预制超声波TIG焊技术 核岛辅助管道管径相对较小、壁厚较薄,可以预制的焊口数量大,传统辅助管道预制焊接采用手工TIG焊技术,管道在焊接之前需要开坡口,然后逐层填充焊丝完成焊接。超声波TIG复合电弧焊原理是将超声波通过导电电极传导到焊接电弧上,在施加超声波后,电弧产生明显的收缩现象,从而提高焊接电弧挺度,增加焊接熔深,从而实现管道不开坡口自熔(见图5)。
 图5 目前,中核二三公司通过开展超声波TIG自动焊接工艺研发实现了6mm壁厚管道预制不开坡口一次性焊透,并在民用化工项目管道预制现场进行了初步应用,在确保质量的前提下有效提高了焊接效率。随着我国核电建造标准升级,该技术可以推广应用于核岛辅助管道预制,对于提高我国核工程管道预制自动化水平具有重要意义。
三、自动熔化极气体保护焊技术
核电站大型罐体、厚壁钢制容器以及大型结构模块安装存在大量规则焊缝,焊接工作量大,采用传统手工焊效率低,质量不容易保证,是自动焊技术的主要研发应用对象。 钢制安全壳(CV)是三代核电AP1000/CAP1400堆型核岛最后一道安全屏障,建造标准要求高。CAP1400核电钢制安全壳容器直径43m,高73.6m,板厚43~55mm,焊缝总长约4 500m,消耗焊材约70t,目前钢制安全壳焊接方法采用钨极氩弧焊和焊条电弧焊联合焊接技术,生产效率低,焊缝质量容易受到焊工操作技能的影响,不容易保证。 中核二三公司于2013年针对钢制安全壳(CV)启动了自动熔化极气体保护焊(简称GMAW)技术研究,利用混合气体作为保护气体,采用连续等速送进可熔合焊丝与焊件之间的电弧作为热源来熔合焊丝和母材金属,形成熔池和焊缝。经过数据统计,采用自动焊技术焊接效率比手工焊提高1倍,焊材消耗量比手工焊减少1/3(见图6)。该技术于2015年12月在山东荣成CAP1400示范工程开始了国内首次应用,填补了我国核电建设安装领域大型容器应用自动焊技术的空白。
 图6 此外,AP1000三代核电机组建造最显著的特点是模块化施工,AP1000核电堆型中的7大结构模块在安装过程中存在大量有规则的焊缝。目前,这些结构模块焊接主要采用手工焊技术,劳动效率低、工作强度大,对焊工的技能水平要求高。通过针对结构模块开展(GMAW)熔化极气体保护自动焊技术研究,开发出针对不同焊接位置的全套自动焊接工艺,在提高焊接质量和效率的同时降低了工人劳动强度(见图7)。
 图7 四、结语
随着焊接技术水平不断进步,采用先进高效的半自动和自动焊技术代替手工焊技术仍是未来发展的趋势。同时,伴随着自动化焊接技术的应用范围逐步扩大,焊丝也将逐步取代焊条成为核电建造的主要焊接材料。在焊接新技术的研发和推广应用过程中,需要采用产、学、研、用联合的模式,掌握焊接标准、焊接材料、焊接工艺、焊接设备及辅助工装成套技术。同时,安装单位、设计院、工程公司和业主公司加强沟通互动,各方联合推动,才能将这些新技术更好更快的应用于现场,提高我国核电建造整体安装技术水平。
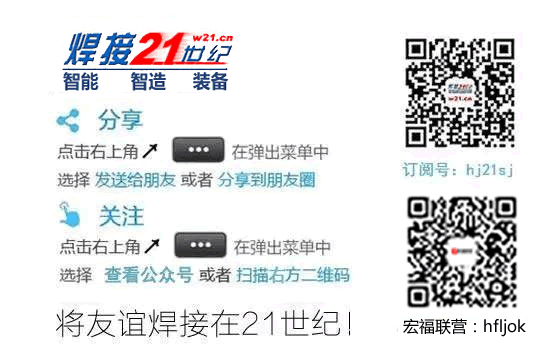 |