铝合金激光焊接工艺是近十几年来发展起来的一项新技术,与传统焊接工艺相比,它具有功能强、可靠性高、无需真空条件及效率高等特点。 其功率密度大、热输入总量低、同等热输入量熔深大、热影响区小、焊接变形小、速度高、易于工业自动化等优点,特别对热处理铝合金有较大的应用优势。 可提高其加工速度并极大地降低热输入,从而可提高生产效率,改善焊接质量。在焊接高强度大厚度铝合金时,传统的焊接方法根本不可能单道焊透,而激光深熔焊时形成大深度的匙孔,发生匙孔效应,则可以得到实现。
一、激光焊接铝合金的优势
1、能量密度高,热输入低,热变形量小,熔化区和热影响区窄而熔深大; 2、冷却速度高而得到微细焊缝组织,接头性能良好; 3、与接触焊相比,激光焊不用电极,所以减少了工时和成本; 4、不需要电子束焊时的真空气氛,且保护气和压力可选择,被焊工件的形状不受电磁影响,不产生X射线; 5、可对密闭透明物体内部金属材料进行焊接; 6、激光可用光导纤维进行远距离的传输,从而使工艺适应性好,配合计算机和机械手,可实现焊接过程的自动化与精密控制。
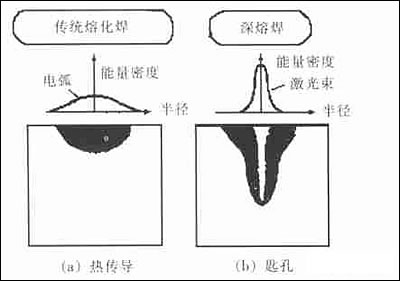 图1 激光焊接时的小孔形状 现在应用的激光器主要是CO2和YAG激光器,CO2激光器功率大,对于要求大功率的厚板焊接比较适合。但铝合金表面对CO2激光束的吸收率比较小,在焊接过程中造成大量的能量损失。YAG激光一般功率比较小,铝合金表面对YAG激光束的吸收率相对CO2激光较大,可用光导纤维传导,适应性强,工艺安排简单等。 在焊接大厚度铝合金时,传统的焊接方法根本不可能单道焊透,而激光深熔焊时形成大深度的匙孔,发生匙孔效应,则可以得到实现。图1为激光焊接时的小孔形状。图2为激光深熔焊示意图。
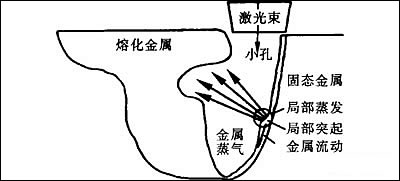 图2 激光深熔焊示意图 铝及铝合金的激光焊接难点在于铝及铝合金对辐射能的吸收很弱,对CO2激光束(波长为10.6m)表面初始吸收率1.7%;对YAG激光束(波长为1.06m)吸收率近5%。图3为不同金属对激光的吸收率。
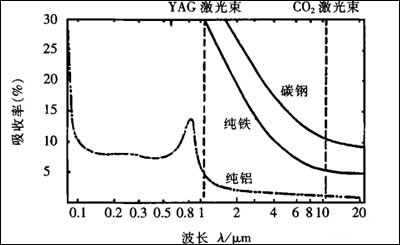 图3 不同金属对激光的吸收率 二、激光焊接铝合金需要注意哪些问题?
1、由于吸收率小,热导率高,在实际铝合金焊接过程中,一定要保证良好的光束聚焦,同时还要用高功率密度的高能激光束进行照射。 2、铝合金激光焊接时,产生深熔焊,激光功率必须达到一个特定的阈值,这就对激光器提出一定的要求,也是激光焊接的一个难点。铝合金的电离能低,部分牌号焊接过程中光致等离子体易于过热和扩散,焊接稳定性差。 3、焊接铝合金就一定要求激光束的能量密度高和光束的聚焦性能好。铝合金是典型的共晶合金。在激光焊接的快速凝固过程中更容易产生热裂纹。激光焊接熔池深宽比大,气泡不易上浮析出,容易产生气孔。 4、液态铝合金的流动性好,表面张力低,焊接过程的不稳定造成焊接熔池剧烈震荡,易产生咬边、成形不连续,严重时造成焊接过程中的小孔突然闭合,而在焊缝中产生直径较大的工艺孔洞(ProcessHoles),或小孔在闭合前由向外喷发的等离子体将液态金属吹出熔池而形成所谓的喷射孔洞(Blowholes)。
  |